I go behind the scenes at TAP’s maintenance hangars in Lisbon
Links on Head for Points may support the site by paying a commission. See here for all partner links.
Air travel has become so routine these days that it’s easy to forget the amount of work that goes in to ensuring a safe and punctual trip.
Even smaller aircraft such as the Airbus A320 family have over 340,000 components, each essential in ensuring the aircraft can reach its destination safely. That’s 340,000 parts that could develop a fault or cause an accident.
TAP invited a group of UK travel writers to Lisbon to take a look behind the scenes at how aircraft maintenance is done. Whilst not strictly ‘miles and points’ related, we couldn’t resist. I also got to chat to the CEO of TAP as you may have read earlier in the week.
TAP’s maintenance operation at Hangar 6
TAP operates its own maintenance base at Lisbon Airport. It’s just five minutes’ walk from the terminal, but it’s lashing with rain on the miserable Thursday I arrive. Mário Lobato de Faria – the Chief Technical Officer – picks us up in his Audi for the quick drive to TAP’s HQ.
Most of this site was built out in the 1970s, not exactly an era of inspiring office architecture. “Welcome to Moscow,” jokes André from TAP’s PR department.
The inside is like stepping back in time to the 1970s. Not that I was around in the 70s, but it’s how I imagine it: dark wood panelling, lots of large individual offices (no hot desking here!) and delightfully vintage furniture. The only thing missing is a heavy cloud of cigar smoke.
These are the offices attached to Hangar 6, the largest of (you guessed it) six aircraft hangars that TAP operates at Lisbon Airport. This one is the newest – the others are smaller and from earlier periods of TAP’s 77-year history.
Across Lisbon Airport, TAP has capacity for eight aircraft in its hangars, although this can stretch to more if the larger ones are out. Arranging them is a game of tetris, especially as newer aircraft come with bigger and bigger winglets, which make it harder to slide one aircraft under the wing of another.
On this Thursday, there are two A330-900neo aircraft plus a handful of smaller A320s all cocooned from the grim weather outdoors. The A330neos are arranged wingtip-to-wingtip – their 64m span is a not inconsiderable 4m longer than the older A330s they replace – and the engineering staff have managed to squeeze in a couple of A320s between them. One is just under their wingtips whilst the other is tucked at the rear of the fuselage.
Just a few feet more and they’d be touching, which would necessitate further safety inspections. Fortunately, Mario’s team are seasoned professionals at these tessellation olympics.
All aircraft go through regular maintenance checks to ensure they’re air worthy, called A, C and D checks. These are like MOTs but on a much, much bigger scale. D checks are the most intensive and involve taking apart almost the entire aircraft every six years and meticulously checking all components.
TAP doesn’t have the capacity to do these – each D check takes weeks and a huge amount of engineering capacity – so TAP focuses on the more regular, less intensive A and C checks that can be done in a few days between flights.
‘A’ checks are performed every eight to ten weeks and involve maintaining key flight controls. This can involve replacing filters, inspecting emergency equipment such as the inflatable slides and making sure all the hydraulics are working smoothly and as intended. ‘A’ checks are normally completed within 24 hours or so and mean that the aircraft can return to service quickly.
‘B’ checks are a bit more involved and take place every two years. These require taking an aircraft out of service for a couple of weeks, which can often be an opportunity to refurbish the cabin too.
The two TAP A330neos we see are currently undergoing these checks, so they should be back in service shortly.
Since they’re grounded, we can get especially close to the Rolls Royce Trent 7000 jet engines which have been designed to be 6dB quieter and 10% more fuel efficient than the engines they replace. Jumping up and sitting in them gives you a sense of the scale of these machines:
One of the A330s is having its engines inspected. To make things easier, the casing can be opened up like the wing casing on a beetle to expose the internal systems. With it opened like this, it makes you realise how complex they are:
Onboard, the cabin is getting a bit of TLC too. The business class cabin (TAP calls it ‘Executive’) looks brand new, to the extent that I have to double check this isn’t a brand-new aircraft (it’s not). TAP is using the time on the ground to replace some items such as the seat belts and buckles, as well as a number of overhead cabin bins. It all looks very smart.
Whilst the aircraft is grounded we also get the opportunity to see into parts of the plane that most passengers never see, including the cockpit and the crew rest area. This is where the crew come for their legally-mandated rest periods throughout the flight, which lets them get some sleep.
On most long haul aircraft, including the A350, the crew rest is above the passenger cabin in the space between the ceiling and the fuselage. On the A330neo, however, Airbus has put it underneath in the cargo hold.
It’s accessible from one of the bulky cabin monuments that you could confuse for a lavatory or galley. It’s down a steep set of stairs:
Inside, there are eight bunks with full-size single beds: two for the flight crew and the remainder for the cabin crew.
Each bunk has a curtain and reading light, as well as a seatbelt. It’s very cosy!
Underneath the cabin is the cargo hold:
…. and, right beneath the cockpit, the avionics bay. This is basically the nerve centre for the aircraft, with racks upon racks of computers packaged in cases that can be quickly removed and swapped out:
The maintenance program is supported by a team of engineers and technicians in nearby buildings. A component shop, next door, can take parts from the aircraft to test and if necessary replace. These can range in size from small nuts and bolts:
…. to massive landing gear struts.
Each needs to be cleaned first before it can be tested. I’m told that’s the job the staff hates, especially when it comes to these things:
Recognise them? 😉
If something needs replacing, the component must be tested before it goes back to the aircraft. This can involve all sorts of things being done to it in these retro-looking test suites:
One of the facilities has been recently refurbished at a cost of €800,000. This piece of kit can test the compression strength of components with a vast array of sensors:
These days, jet engines are as complicated as the rest of the aircraft combined. Here you’ll find a number of engines in various states of assembly.
At TAP, they primarily deal with the CFM engines for the A320 family aircraft. The Rolls Royce Trent 7000 that powers the A330neos is too big to be done here.
The fan blades from the front of the engine can be individually removed, checked and tested.
TAP Maintenance and Engineering is working towards being able to overhaul the CFM Leap engines from the A320neos. You can see just how far the technology has come just by looking at the front. Old:
vs new:
The newer turbofan features fewer fanblades but these are more elegantly sculpted out of carbon fibre. The old CFM 56 engine looks almost antique in comparison.
Once an engine has been reassembled it needs to be tested, and TAP has its very own test stand. This is where the performance of the engine is tested over the course of 3+ operational hours.
TAP’s test bed is only big enough for smaller, single aisle jet engines but it’s still vast:
Air is sucked from a vertical structure before being filtered for any particles or, dare I say, birds. It passes horizontally through the jet before being blasted into an exhaust pipe that re-directs it up and out.
Walking through TAP’s maintenance hangars I was reminded of the complexity of the aircraft we all regularly fly on. It’s a miracle that airplanes even get off the ground when you see the number of components and processes that have to be followed.
As Mario says, “at the end of the day the passenger only sees two things – on time performance and the cabin. But it’s a lot that goes into it.” I think that might be an understatement.
PS. If you are not a regular Head for Points visitor, why not sign up for our FREE weekly or daily newsletters? They are full of the latest Avios, airline, hotel and credit card points news and will help you travel better. To join our 65,000 free subscribers, click the button below or visit this page of the site to find out more. Thank you.
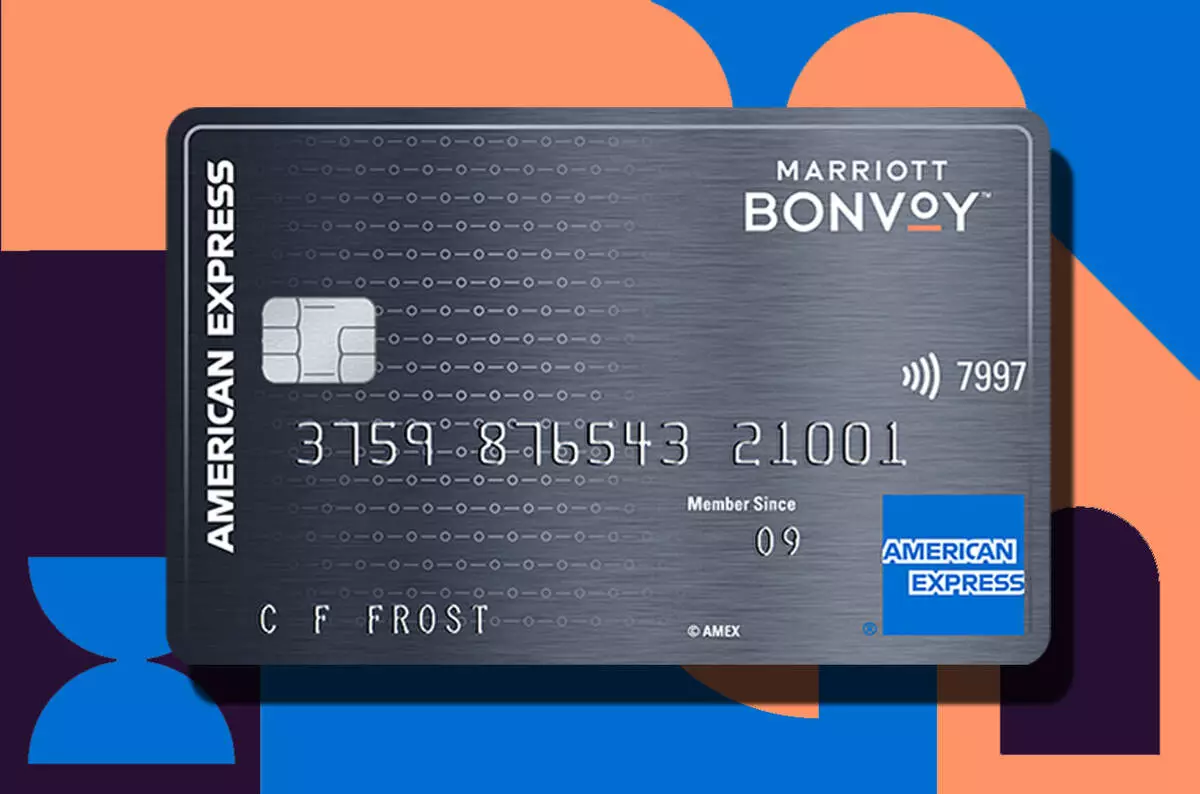
How to earn Star Alliance miles from UK credit cards (April 2025)
None of the Star Alliance airlines currently have a UK credit card.
There is, however, still a way to earn Star Alliance miles from a UK credit card.
The route is via Marriott Bonvoy. Marriott Bonvoy hotel loyalty points convert to over 40 airlines at the rate of 3:1.
The best way to earn Marriott Bonvoy points is via the official Marriott Bonvoy American Express card. It comes with 20,000 points for signing up and 2 points for every £1 you spend. At 2 Bonvoy points per £1, you are earning (at 3:1) 0.66 airline miles per £1 spent on the card.
There is a preferential conversion rate to United Airlines – which is a Star Alliance member – of 2 : 1 if you convert 60,000 Bonvoy points at once.
The Star Alliance members which are Marriott Bonvoy transfer partners are: Aegean, Air Canada, Air China, Air New Zealand, ANA, Asiana Airlines, Avianca, Copa Airlines, Singapore Airlines, TAP Air Portugal, Thai Airways, Turkish Airlines and United Airlines.
You can apply here.

Marriott Bonvoy American Express
20,000 points for signing up and 15 elite night credits each year Read our full review
Comments (69)